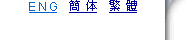 |
|
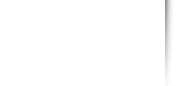 |
 |
BizVerify |
|
Luen Cheong Printing Equipment Group Limited |
Verified By : SMR |
Verified Date : 2008-11-17 |
|
 |
|
|
|
|
|
|
|
|
|
|
|
|
MARABU INK SR DryingPhysically very fast drying,dries at 20? air temperature within 5-10min to be overprinted,at 50? in a tunnel dryer and stackable within 20-30 sec.With high dryer capacity and good ventilation provided,the drying temperature can be lowered to 40?,for less material distortion.If the SR is mixed with hardener PUH,the drying time and block resistance of the ink is reduced.Stress resistanceAfter proper and thorough drying,the ink film exhibits outstanding adhesion as well as rub,scratch,and block resistance and is weldable(SR 173 Black).SR colour shades have a high chemical resistance to petrol(except SR170).Due to its high pigmentation,Opaque White SR170 is unsuitable for moulding.Please use White SR070 or SR270 instead.To achieve a maximum rub resistance,the SR can be overvarnished with printing varnish SR910 or SR911.
Marapol PY is mainly used to print onto packaging containers of PE or PP and onto rigid PVC-types.When printing onto PE and PP,the surface of the substrate must be pre-treated in the usual way,either by flaming or by Corona discharge.According to our experience,the PY adheres on polyolefines with a minimum surface tension of 42-48mN/m.PY can also be processed with a spray gun,but preliminary trials are necessary for this process.We recommend to filter the thinned press-ready ink(25?m screen)before processing it,as otherwise there could be bubbles in the ink film.
Drying Physically fast drying,dries at 20? within 20 to 30 min.(for overprintability),at 50? in a tunnel dryer within 30-60sec.The times mentioned vary according to thickness of the ink film,with or without addition of hardener and type of hardener,drying conditions and auxiliaries used.Please note that the drying speed slows down i shades are overprinted and a hardener has been used. Stress resistance After proper and thorough drying,the ink film exhibits outstanding adhesion as well as rub and scratch resistance and is resistant to oils,greases,diluted acids and bases,and alcohol. |
|
|
|
|
|
|
<script src="http://www.google-analytics.com/urchin.js" type="text/javascript">
</script>
<script type="text/javascript">
_uacct = "UA-1430666-1";
urchinTracker();
</script> |
|
|
In the printing process, the ink often considered the printing quality is affected the most crucial factor. However, other factors control is also important, the printing staff often caused by other factors attributed to problems in the printing ink, they sometimes have to spend a few hours can not solve the problem, mainly because they ignored the other variables such as machinery installed, Environmental conditions and other factors. Therefore, the printing staff to the process of printing inks and thoroughly understand the role of the problems arise, will affect the quality of all the factors are taken into account, rather than blindly looking for ink aspects of the A type of printing ink .
Devoted to the printing ink different from the general solvent-based inks, water-based inks and uv light-cured screen printing ink. Although the silk screen printing inks and ink have some similar characteristics, but they still have great differences. And silk screen printing ink different from printing ink to dry faster speed, this is also printing ink most prominent feature. At the same time, printing inks are often printed on the film, which uses lead to printing ink is vulnerable to a number of factors such as temperature, humidity and the impact of static electricity. Specialized preparation for the printing ink, including one component of the ink, two-component ink, Kaogan type of ink-and-such as sublimation.
1) one-component ink
One component ink (also known as volatile solvent-based inks) on the drying of volatile solvents, inks do not necessarily have to join such a catalyst. One component of ink and non-shiny gloss of the two, they are mainly used for the printing of plastic printing.
2) two-component ink
Ink also called two-component chemical reaction of ink, printing must join before the catalyst, catalyst and ink resin in the reaction, through polymerization to achieve the objective of ink drying.
Will be used in the printing of two-component ink, it is necessary to add a certain percentage of catalyst, usually used to measure the weight. Add the catalyst ratio must be strictly controlled, the excessive increase would significantly reduce the ink "adaptation period" of the increase is too small, may result in the ink drying time of less than the best dry performance. Generally speaking, if the deployment of ink and catalyst of misconduct, will lead to uneven and printing ink attached to the image durability of printed materials, such as lack of defects.
3)-ink Kaogan
Kaogan-ink divided into two types: one is the standard two-component ink on the basis of adding another catalyst, another is used for the deployment of special glass, ceramics and metals, such as printing of the ink. As its name, Kaogan-ink must be heated to a certain temperature and dry. Use this time to calculate the ink drying time, the higher the temperature, the shorter the drying time, but the drying temperature is too high will have a Mexican film brittle, so be flexible in ink to maintain the temperature Kaogan ink.
4) type of ink
Oxidized ink absorption of oxygen in the surrounding environment polymerization to form a Mexican film, do not need to add a catalyst. Oxidation is a typical application of ink printing of flexible packaging and printing of synthetic materials, such as rubber or keyboard. Because of the dry-ink slow, long time, the use of the limited.
5)-sublimation inks
- Sublimation inks used in the process of the need for special processing is to be printed after its heating, so that printing of showing a porous, so that when exposed to heat the dye printing of the surface, the ink in the dye into a gaseous state and then Access to printing on the surface, actually changed the printing of the color. Once the printing of cooling after the printing ink on the Mount of the surface.
Sublimation inks the most common type of computer keyboard printing, as well as those of oil, the higher the wear-resistance requirements of print, which is used by the two-component ink has not been. The problem is particularly noteworthy because of sublimation ink is actually changed the printing of the color, so printing ink and color of the match more difficult. Therefore printing of color to the final than the color printing needs from shallow, because the sublimation of darker color ink in the printing of color changes on the surface are often less obvious.
6) Special inks and additives
Printing ink, including special edible ink, silicon-resin inks, lubricants and Mexico, corrosion resistance ink, conductive inks and uv light-cured inks, these rapidly changing ink stick will be the ability to decide whether the ink can be effectively transferred to the printing of the surface. Meanwhile, in order to adjust the ink Printability and performance, in addition to add solvents and catalysts, but also may use a lot of additives, such as viscosity-Mexican agents, antistatic agents, rheological agent. But the use of additives printing ink will have a great impact on performance, when used to move constant.
2 printing printing process
The first step, the printed version of the etching Depression regional add ink, this marks the beginning of the printing cycle (Figure 1). Some printing machines used Zhumo the opening hole, while some use of closed Zhumo hole (such Zhumo hole to prevent solvent in??hole in the volatile out). At this time the ink viscosity must be low enough so that the ink can be formed to rollout in the printed version of the transfer on the surface, and can image etched into the depression in the region.
The second step, scraping by Dao printing ink printed version of uplift of the (blank) on the ink Guagan Jing, the only ink etched into the image of the Depression in the region. Because of the volatile solvents very quickly, this will lead to depression image of the ink on the surface than below the ink stick to some.
The third step, the first printing to the rolling gravure evenly exert pressure on the gravure at the same time to air out. At this time because of depression image in the region of the ink viscosity larger surface, so the ink can leave the region etched depression in the printing and mount the head.
The fourth step, the first to leave when the printing gravure printing, the surface of the first printing ink in the volatile solvent swap, which makes printing the first surface layers of ink have become more Nien.
Step 5, when the printing of the first printing of the surface exposed to the surface, the surface because of the first printing ink viscosity, so that was the first printing ink from the printing and adhesion of the surface. In this step, although the first printing may impose very big pressure, but is designed as a first printing of the arc and flexible, so that images can be flat surface rather than means of contact with the printing. In fact, a proper design and printing of the first printing of contacts will not be a 0. Kok, which would prevent residues in the air and the first printing of the letterhead, and if the residual air in the image of the resulting image will not completely transfer.
Step 6, the printing of the letterhead of the first to leave the surface of restitution. If these six steps involved in the changes in factors can be properly controlled, the first printing will leave the printing of clean, then a complete printing cycle ended, and the first printing prepare for the next printing cycle.
From the above six steps can be seen, printing ink by the inherent characteristics of this is a significant variable ink stick is the ability to highlight and paint pigment particle size and proportion with other types of ink vary greatly. Many in the gravure printing the image etched a depth of 25 u tn, or even smaller. If this is the case, contained in the printing ink pigment particles to be than most of the small screen printing ink. In addition, since the printing of the printing ink film thickness is about 20 percent of screen printing, in order to obtain sufficient Zhegai Li, printing ink in the pigment concentration must be high enough.
Since the printing ink on the changing requirements of viscosity is very high, making printing ink solvents used in the volatile rate than ordinary screen printing ink solvents used by the much faster, it will be difficult to get good printing results.
3 printing ink deployment
In general, ink is ink production Chamber of Commerce which apply to the printing of guidance, but such views for reference purposes only. To select a suitable ink, need to understand several things: What kind of printing; printing of the need for printing before the pretreatment; India needs what kind of color ink abrasion resistance, chemical resistance, the climate of tolerance , And other printing requirements and the ink drying or curing the recommendation of the way.
Once selected for the printing of the ink, we must remember that in accordance with the ink manufacturers recommend ways to deploy ink. A lot of ink manufacturers have provided a technical information brochures, above ink can be compatible with the catalyst, additives and solvents, inks and the deployment of the correct ratios. Many ink deployment is to deploy by weight, rather than by volume to the deployment, so the best use of a precision weighing at least o. 1 g digital equipment to precisely that weight. To make a color, it should be able to use a precision to o. o1g the equipment to weigh, such tests could have been avoided color ink waste.
The right to be additive mixed with the ink, the ink is the best time to dilute the consistency can be a suitable solvent or some solvent to dilute the mixture. Standard printing ink usually have a choice of a suitable dilute, including the volatile fast, slow three dilute agent. Ink manufacturers have a general add value to dilute the scope of the general ink by the ratio of 10% to 20% to dilute the agent added.
Decide which dilute the number of agents and add dilute agent, for most people is a guess, this is not correct. At the beginning of the printing of a batch of live, to conduct the trial of dilute. First of all the printing machinery in the printing speed of the need to adjust the speed of the first printing of the pressure regulator to look at the best condition. Then you can test, first of all to join a rate of evaporation of water down the middle, add a recommendation for the proportion of the value of the intermediate value. For example, if the recommendation of the value is 10-20%, add 1 5% of the diluted agent. To try to print several times so that the etching gravure fully wetting and to allow appropriate expansion of the first printing, at least on trial in the printing of India 1 2 times, it is necessary to adjust the pressure of the first printing. If printed out the image quality, you can use the following two steps to test.
Step one: take a normal printing speed printing out under the image, turn off the presses. Check printing heads of the images, using a small mirror to observe the first printing of the image below. Check printing head of the image is complete and image position is correct. If the head of the printing images no problem, to the second step. (Note: If the head of the printing images of the lost, or appear to have Ju Chizhuang Edge, the general is due to the ink is too thick. Watered down by adding a certain number of agents, to repeat this work until the head was in the printing Acceptable image: If it is found that the image printing head position it should not in the position,
The first printing of the location to adjust. ) Step 2: If the head of the printing images no problem, then, in the normal operating speed of the printing to the printing of images on. If the quality can also print, you can start printing production if printing out the images look a bit dirty, transparent, or fuzzy, and printing ink is also attached to the head, ink that is too thin. Can increase a small amount of ink, printing speed can be reduced.
Ink in control of the process, attention should be paid temperature and relative humidity on the performance of ink is a big, the higher the temperature, the sooner the volatile solvent, ink stick of change sooner. However, the relative humidity of the two extremes (very high humidity and humidity is very small) is not such a situation. Relative humidity of the two extremes is in the printing presses on the control of ink when a headache. Humidity over 80 -85% change viscosity of the ink will become very slow speed i and humidity below 1 5 ~ 2o% will also ink change the viscosity is very slow. But the environment at the two extremes, the only control the characteristics of ink solvent ink to improve the viscosity of the basic powerless.
For some often-repeated printing of live pieces, can be a way to speed up the deployment process of ink, this method known as the Mexican-matrix method. If the printing of each shipment of live pieces are printed using the same speed, you can use a chart printed record of each shipment of live pieces of the temperature and humidity, temperature, as a shaft, relative humidity as another axis. The two directions of the intersection points added to print an acceptable quality of printing by the need to dilute the proportion of. For a period of time to collect enough information, can be directly from Table 1 (see below) View without trial again
At the beginning, you may think that collect and record information to spend too much time. In fact, after some time you will find this method of saving time than the time it takes to gather information much more. And, with this form will enable the deployment of ink become more simple.
4 printing environment control
We have seen the process of printing ink of the importance of control. However, the printing quality to meet the requirements of the printing publications, must be given all the factors in control. First of all, this ink from the printing machines and the regulation started.
As the map shown in Figure 6 to 1, on Mexico, scraping ink, printing ink and the suction head in the course of image transfer, printing ink and the machine will be a lot of changes. Printing of each step in certain areas and are «different, so to particularly pay attention to regulate printing machine, each time for the need to regulate access to all the printing results, it is necessary to control environmental conditions, the speed of printing machines , Gravure printing the etching depth and quality of etching, the first printing of the hardness and rebound.
In need of printing speed, as well as the minimum necessary for the first printing after good pressure regulator, the next question to consider is the printing environment.
Printing workshop temperature and relative humidity every day, is subject to change. Study found that printing is the best environment: temperature between 20 ~ 22 ?, and the relative humidity at 50-60%. However, in the real working environment, we rarely achieve the best possible working environment. Temperature and relative humidity changes will obviously affect the entire printing process, it is necessary to minimize environmental factors on the impact of printing process.
If the printing shop and storage ink, printing of, additives, printing workshop in the first class of materials no environmental regulation and control facilities, here are some ways in the printing process so that environmental problems caused by changes to minimize factors:
(1) the machines and materials put in the walls of the room far away from some. Room wall is the more significant temperature change places. Day or seasonal variations in the temperature here more.
(2) Do not let machinery and materials by exposure to direct sunlight, air conditioning and avoid the heat flow of direct air and air-conditioning Chuidao machines and materials.
(3) to live with a number of pieces need to use the printing ink, printing head, catalyst, printing of stored in the same place. If there are no such conditions and in a few hours before the printing of these materials into the printing workshop in. In this way, ink, printing, etc. can be printed in advance and workshop environment to avoid the emergence of some printing problems. Because the material from a thermal environment suddenly into the colder environment, will unite in response, while printing of the water will be seen tremendous changes.
(4) tried to keep the environment clean workshop. Even the packaging materials Doula in the dust, if entered in ink or in the first printing will also be printed on the face of lower quality. Frequently used vacuum cleaners and mop Tuoxi printing workshop, to maintain clean air, remember not to use a broom and dust that would float to the printing press and printing materials. In addition, the printing workshop for local clean, use vacuum cleaners to remove dust, rather than use air conditioning, which will expand the scope of the dust.
5 Conclusion
Although the control and maintain the correct ink performance looks very complicated, this is not the case. By carefully regulating the correct printing machine and environmental change and other factors, the problems arise, the comprehensive consideration could lead to problems of various factors on the emergence of numerous problems can be avoided, even if there are problems can also be the right remedy. |
|
|
In the printing process, the ink often considered the printing quality is affected the most crucial factor. However, other factors control is also important, the printing staff often caused by other factors attributed to problems in the printing ink, they sometimes have to spend a few hours can not solve the problem, mainly because they ignored the other variables such as machinery installed, Environmental conditions and other factors. Therefore, the printing staff to the process of printing inks and thoroughly understand the role of the problems arise, will affect the quality of all the factors are taken into account, rather than blindly looking for ink aspects of the
A type of printing screen printing ink
Devoted to the printing ink different from the general solvent-based inks, water-based inks and uv light-cured screen printing ink. Although the silk screen printing inks and ink have some similar characteristics, but they still have great differences. And silk screen printing ink different from printing ink to dry faster speed, this is also printing ink most prominent feature. At the same time, printing inks are often printed on the film, which uses lead to printing ink is vulnerable to a number of factors such as temperature, humidity and the impact of static electricity. Specialized preparation for the printing ink, including one component of the ink, two-component ink, Kaogan type of ink-and-such as sublimation.
1) one-component ink
One component ink (also known as volatile solvent-based inks) on the drying of volatile solvents, inks do not necessarily have to join such a catalyst. One component of ink and non-shiny gloss of the two, they are mainly used for the printing of plastic printing.
2) two-component ink
Ink also called two-component chemical reaction of ink, printing must join before the catalyst, catalyst and ink resin in the reaction, through polymerization to achieve the objective of ink drying.
Will be used in the printing of two-component ink, it is necessary to add a certain percentage of catalyst, usually used to measure the weight. Add the catalyst ratio must be strictly controlled, the excessive increase would significantly reduce the ink "adaptation period" of the increase is too small, may result in the ink drying time of less than the best dry performance. Generally speaking, if the deployment of ink and catalyst of misconduct, will lead to uneven and printing ink attached to the image durability of printed materials, such as lack of defects.
3)-ink Kaogan
Kaogan-ink divided into two types: one is the standard two-component ink on the basis of adding another catalyst, another is used for the deployment of special glass, ceramics and metals, such as printing of the ink. As its name, Kaogan-ink must be heated to a certain temperature and dry. Use this time to calculate the ink drying time, the higher the temperature, the shorter the drying time, but the drying temperature is too high will have a Mexican film brittle, so be flexible in ink to maintain the temperature Kaogan ink.
4) type of ink
Oxidized ink absorption of oxygen in the surrounding environment polymerization to form a Mexican film, do not need to add a catalyst. Oxidation is a typical application of ink printing of flexible packaging and printing of synthetic materials, such as rubber or keyboard. Because of the dry-ink slow, long time, the use of the limited.
5)-sublimation inks
- Sublimation inks used in the process of the need for special processing is to be printed after its heating, so that printing of showing a porous, so that when exposed to heat the dye printing of the surface, the ink in the dye into a gaseous state and then Access to printing on the surface, actually changed the printing of the color. Once the printing of cooling after the printing ink on the Mount of the surface.
Sublimation inks the most common type of computer keyboard printing, as well as those of oil, the higher the wear-resistance requirements of print, which is used by the two-component ink has not been. The problem is particularly noteworthy because of sublimation ink is actually changed the printing of the color, so printing ink and color of the match more difficult. Therefore printing of color to the final than the color printing needs from shallow, because the sublimation of ink in the darker color printing on the surface of the color changes are often less obvious.
6) Special inks and additives
Printing ink, including special edible ink, silicon-resin inks, lubricants and Mexico, corrosion resistance ink, conductive inks and uv light-cured inks, these rapidly changing ink stick will be the ability to decide whether the ink can be effectively transferred to the printing of the surface. Meanwhile, in order to adjust the ink Printability and performance, in addition to add solvents and catalysts, but also may use a lot of additives, such as viscosity-Mexican agents, antistatic agents, rheological agent. But the use of additives printing ink will have a great impact on performance, when used to move constant.
2 printing printing process
The first step, the printed version of the etching Depression regional add ink, this marks the beginning of the printing cycle (Figure 1). Some printing machines used Zhumo the opening hole, while some use of closed Zhumo hole (such Zhumo hole to prevent solvent in hole in the volatile out). At this time the ink viscosity must be low enough so that the ink can be formed to rollout in the printed version of the transfer on the surface, and can image etched into the depression in the region.
The second step, scraping by Dao printing ink printed version of uplift of the (blank) on the ink Guagan Jing, the only ink etched into the image of the Depression in the region. Because of the volatile solvents very quickly, this will lead to depression image of the ink on the surface than below the ink stick to some.
The third step, the first printing to the rolling gravure evenly exert pressure on the gravure at the same time to air out. At this time because of depression image in the region of the ink viscosity larger surface, so the ink can leave the region etched depression in the printing and mount the head.
The fourth step, the first to leave when the printing gravure printing, the surface of the first printing ink in the volatile solvent swap, which makes printing the first surface layers of ink have become more Nien.
Step 5, when the printing of the first printing of the surface exposed to the surface, the surface because of the first printing ink viscosity, so that was the first printing ink from the printing and adhesion of the surface. In this step, although the first printing may impose very big pressure, but is designed as a first printing of the arc and flexible, so that images can be flat surface rather than means of contact with the printing. In fact, a proper design and printing of the first printing of contacts will not be a 0. Kok, which would prevent residues in the air and the first printing of the letterhead, and if the residual air in the image of the resulting image will not completely transfer.
Step 6, the printing of the letterhead of the first to leave the surface of restitution. If these six steps involved in the changes in factors can be properly controlled, the first printing will leave the printing of clean, then a complete printing cycle ended, and the first printing prepare for the next printing cycle.
From the above six steps can be seen, printing ink by the inherent characteristics of this is a significant variable ink stick is the ability to highlight and paint pigment particle size and proportion with other types of ink vary greatly. Many in the gravure printing the image etched a depth of 25 u tn, or even smaller. If this is the case, contained in the printing ink pigment particles to be than most of the small screen printing ink. In addition, since the printing of the printing ink film thickness is about 20 percent of screen printing, in order to obtain sufficient Zhegai Li, printing ink in the pigment concentration must be high enough.
Since the printing ink on the changing requirements of viscosity is very high, making printing ink solvents used in the volatile rate than ordinary screen printing ink solvents used by the much faster, it will be difficult to get good printing results.
3 printing ink deployment
In general, ink is ink production Chamber of Commerce which apply to the printing of guidance, but such views for reference purposes only. To select a suitable ink, need to understand several things: What kind of printing; printing of the need for printing before the pretreatment; India needs what kind of color ink abrasion resistance, chemical resistance, the climate of tolerance , And other printing requirements and the ink drying or curing the recommendation of the way.
Once selected for the printing of the ink, we must remember that in accordance with the ink manufacturers recommend ways to deploy ink. A lot of ink manufacturers have provided a technical information brochures, above ink can be compatible with the catalyst, additives and solvents, inks and the deployment of the correct ratios. Many ink deployment is to deploy by weight, rather than by volume to the deployment, so the best use of a precision weighing at least o. 1 g digital equipment to precisely that weight. To make a color, it should be able to use a precision to o. o1g the equipment to weigh, such tests could have been avoided color ink waste.
The right to be additive mixed with the ink, the ink is the best time to dilute the consistency can be a suitable solvent or some solvent to dilute the mixture. Standard printing ink usually have a choice of a suitable dilute, including the volatile fast, slow three dilute agent. Ink manufacturers have a general add value to dilute the scope of the general ink by the ratio of 10% to 20% to dilute the agent added.
Decide which dilute the number of agents and add dilute agent, for most people is a guess, this is not correct. At the beginning of the printing of a batch of live, to conduct the trial of dilute. First of all the printing machinery in the printing speed of the need to adjust the speed of the first printing of the pressure regulator to look at the best condition. Then you can test, first of all to join a rate of evaporation of water down the middle, add a recommendation for the proportion of the value of the intermediate value. For example, if the recommendation of the value is 10-20%, add 1 5% of the diluted agent. To try to print several times so that the etching gravure fully wetting and to allow appropriate expansion of the first printing, at least on trial in the printing of India 1 2 times, it is necessary to adjust the pressure of the first printing. If printed out the image quality, you can use the following two steps to test.
Step one: take a normal printing speed printing out under the image, turn off the presses. Check printing heads of the images, using a small mirror to observe the first printing of the image below. Check printing head of the image is complete and image position is correct. If the head of the printing images no problem, to the second step. (Note: If the head of the printing images of the lost, or appear to have Ju Chizhuang Edge, the general is due to the ink is too thick. Watered down by adding a certain number of agents, to repeat this work until the head was in the printing Acceptable image: If it is found that the image printing head position it should not in the position,
The first printing of the location to adjust. ) Step 2: If the head of the printing images no problem, then, in the normal operating speed of the printing to the printing of images on. If the quality can also print, you can start printing production if printing out the images look a bit dirty, transparent, or fuzzy, and printing ink is also attached to the head, ink that is too thin. Can increase a small amount of ink, printing speed can be reduced.
Ink in control of the process, attention should be paid temperature and relative humidity on the performance of ink is a big, the higher the temperature, the sooner the volatile solvent, ink stick of change sooner. However, the relative humidity of the two extremes (very high humidity and humidity is very small) is not such a situation. Relative humidity of the two extremes is in the printing presses on the control of ink when a headache. Humidity over 80 -85% change viscosity of the ink will become very slow speed i and humidity below 1 5 ~ 2o% will also ink change the viscosity is very slow. But the environment at the two extremes, the only control the characteristics of ink solvent ink to improve the viscosity of the basic powerless.
For some often-repeated printing of live pieces, can be a way to speed up the deployment process of ink, this method known as the Mexican-matrix method. If the printing of each shipment of live pieces are printed using the same speed, you can use a chart printed record of each shipment of live pieces of the temperature and humidity, temperature, as a shaft, relative humidity as another axis. The two directions of the intersection points added to print an acceptable quality of printing by the need to dilute the proportion of. For a period of time to collect enough information, can be directly from Table 1 (see below) View without trial again
At the beginning, you may think that collect and record information to spend too much time. In fact, after some time you will find this method of saving time than the time it takes to gather information much more. And, with this form will enable the deployment of ink become more simple.
4 printing environment control
We have seen the process of printing ink of the importance of control. However, the printing quality to meet the requirements of the printing publications, must be given all the factors in control. First of all, this ink from the printing machines and the regulation started.
As the map shown in Figure 6 to 1, on Mexico, scraping ink, printing ink and the suction head in the course of image transfer, printing ink and the machine will be a lot of changes. Printing of each step in certain areas and are «different, so to particularly pay attention to regulate printing machine, each time for the need to regulate access to all the printing results, it is necessary to control environmental conditions, the speed of printing machines , Gravure printing the etching depth and quality of etching, the first printing of the hardness and rebound.
In need of printing speed, as well as the minimum necessary for the first printing after good pressure regulator, the next question to consider is the printing environment.
Printing workshop temperature and relative humidity every day, is subject to change. Study found that printing is the best environment: temperature between 20 ~ 22 ?, and the relative humidity at 50-60%. However, in the real working environment, we rarely achieve the best possible working environment. Temperature and relative humidity changes will obviously affect the entire printing process, it is necessary to minimize environmental factors on the impact of printing process.
If the printing shop and storage ink, printing of, additives, printing workshop in the first class of materials no environmental regulation and control facilities, here are some ways in the printing process so that environmental problems caused by changes to minimize factors:
(1) the machines and materials put in the walls of the room far away from some. Room wall is the more significant temperature change places. Day or seasonal variations in the temperature here more.
(2) Do not let machinery and materials by exposure to direct sunlight, air conditioning and avoid the heat flow of direct air and air-conditioning Chuidao machines and materials.
(3) to live with a number of pieces need to use the printing ink, printing head, catalyst, printing of stored in the same place. If there are no such conditions and in a few hours before the printing of these materials into the printing workshop in. In this way, ink, printing, etc. can be printed in advance and workshop environment to avoid the emergence of some printing problems. Because the material from a thermal environment suddenly into the colder environment, will unite in response, while printing of the water will be seen tremendous changes.
(4) tried to keep the environment clean workshop. Even the packaging materials Doula in the dust, if entered in ink or in the first printing will also be printed on the face of lower quality. Frequently used vacuum cleaners and mop Tuoxi printing workshop, to maintain clean air, remember not to use a broom and dust that would float to the printing press and printing materials. In addition, the printing workshop for local clean, use vacuum cleaners to remove dust, rather than use air conditioning, which will expand the scope of the dust.
5 Conclusion
Although the control and maintain the correct ink performance looks very complicated, this is not the case. By carefully regulating the correct printing machine and environmental change and other factors, the problems arise, the comprehensive consideration could lead to problems of various factors on the emergence of numerous problems can be avoided, even if there are problems can also be the right remedy.
|
|
|
|
|
|
|
|